The use of wireless communication technologies is favored by the rise in mobile systems and the transition from static production facilities to a modularized factory structure. It is crucial to use a variety of technologies rather than just 5G.
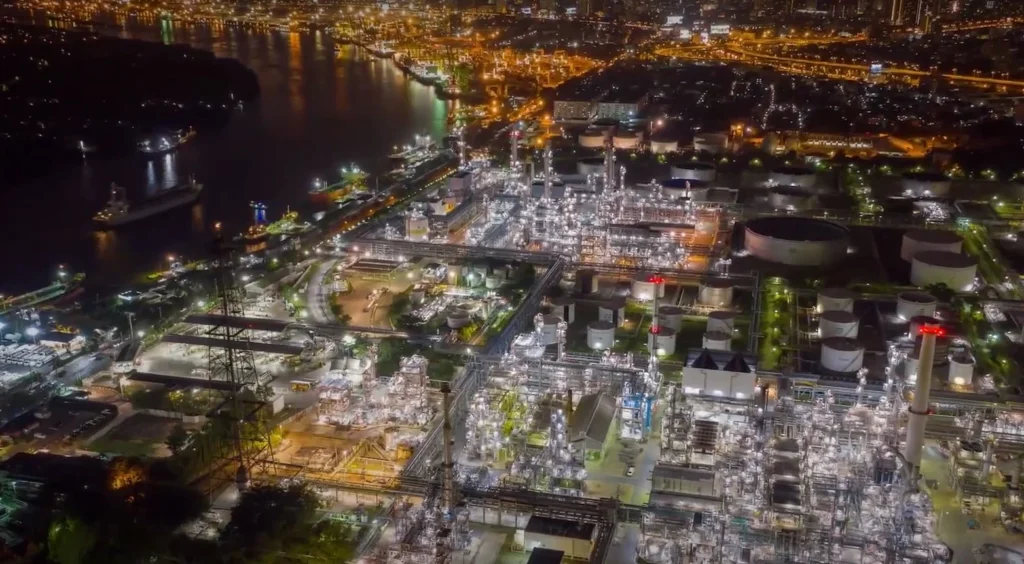
With the help of digitalization, factory automation is currently moving toward Industry 4.0, or an intelligent and connected smart factory. The idea is for a highly flexible, future factory that can handle a wide range of tasks, including batch size flexibility and a wide range of product options.
The requirement for mobility in such an environment rises, for example, with automated guided vehicles (AGV). Man and machine cooperation, such as intelligent logistics solutions, will contribute to the increased flexibility and efficiency of production facilities in the future.
The close-knit communication that links each of these systems is another aspect of this. In the end, the entire value chain must be smoothly incorporated into the factory’s wireless communication systems like ZigBee. Nevertheless, the high technical demands of the future smart factory frequently exceed the capabilities of the wireless communication systems that are currently on the market.
WLAN by itself is insufficient
Automated Guided Vehicles (AGV) mobile systems from SEW-Eurodrive are currently primarily networked via WLAN. However, WLAN will not be able to support AGV use cases in an adaptable production setting in the future. Wireless sensor networks, mobile robots, and mobile control panels with safety features are a few examples of applications whose communication needs WLAN cannot meet.
The creation of matrices as a future standard
One potential idea for the factory of the future is matrix production. It assigns production cells to the steps in the automated production process that are necessary for manufacturing the goods.
Workpieces are fed into a production cell and go through a series of processes (assembly, testing, and modification). After that, the altered workpiece exits the cell. A different product can be made if the workpiece’s path through the factory is altered. This very adaptable concept necessitates exact coordination of every procedure.
Mobile assistant scenarios
Intelligent logistics systems and mobile assistants (MA) make sure that goods are transported between the production cells. They can satisfy the strict requirements of the matrix production concept because they are sophisticated variations of the traditional AGV. They perform a variety of jobs, including direct human support, processing goods, and transportation.
Common uses
Up to 1,000 mobile participants and 100 production cells spread across 10,000 m2 must be connected to wireless communication in an exemplary matrix production. As a result, use cases and goals in the factory of the future are highly varied. For instance, a wireless sensor network uses very little energy to communicate but still transmits very little data.
Unpredictable data rates are produced by control panels. Documents, videos, and emails can all be sent. The chosen communication channel needs to be capable of managing these various loads with ease. Additionally, mobile assistant communication can be highly varied. Here, an operator using remote control should be used as an example. Live video and other sensor data that need a high throughput must be sent from the mobile assistant to the operator.
The mobile assistant receives movement commands from the operator in the opposite direction, and no packet loss is allowed. In order for the operator to control the mobile assistant, low latency is needed for both the uplink and downlink.
Limitations of the technologies available today
An application’s difficulties for the communication system are determined by all of its attributes. As a result, the number of devices in the wireless sensor network presents a challenge rather than the data rate, since only a portion of the nodes need accurate cycle times and low latency.
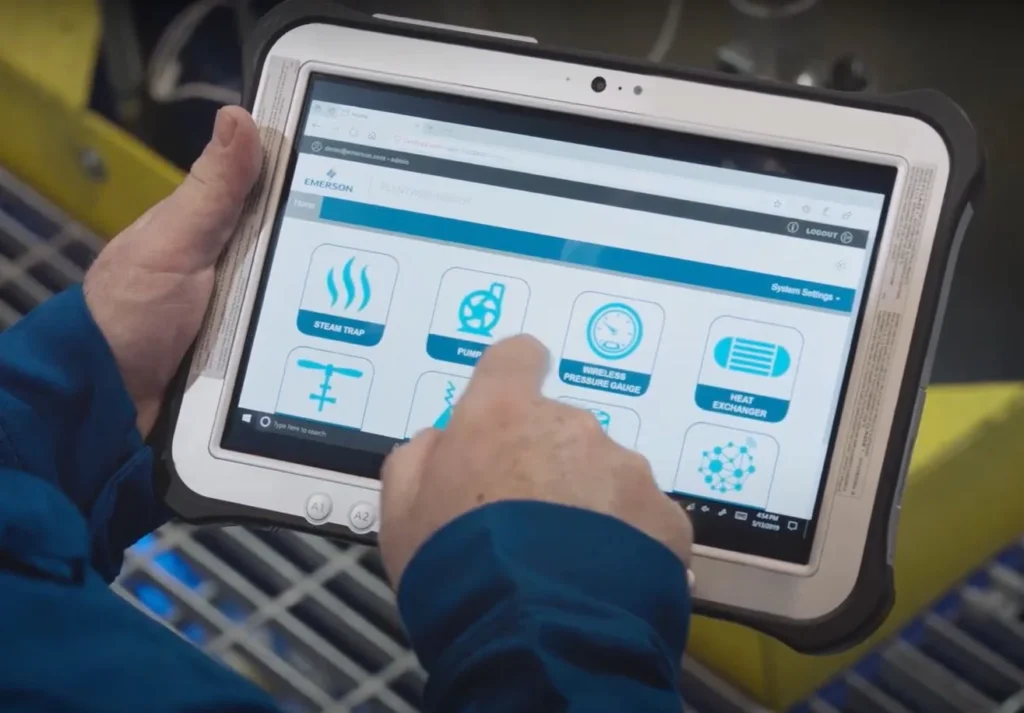
A distinct challenge is that mobile control panels may contain applications that are latency- and reliability-critical in addition to data-intensive. Higher peaks will also occur, but a concurrency factor provides a decent indication of the average data rate in this case.
This also holds true for use cases involving mobile assistants and simultaneity. For certain requests, semi-persistent scheduling is frequently necessary to guarantee low latencies. If not put to use, though, this results in resources being used inefficiently or not at all.
Mobile connectivity in the future factory
Based on ongoing field testing, our example factory with 10,000 m2 of space cannot be fully satisfied by the fifth generation of mobile communications. But, in the event that the network experiences peak loads, for instance, the resources are no longer adequate. In this regard, it would be very interesting to see how the upcoming field tests and Release 16 and 17 of the 5G standard perform.
In conclusion
There is already a lot of interest in 5G + X. On factory floors, the initial implementations are now in progress. Currently, private LTE or 5G non-standalone solutions can be used to obtain first impressions. Although it is not designed for use in factory automation, the 802.11 family of technologies is mature and still fulfills the needs of certain use cases. Flexible routing technologies enable the integration of other state-of-the-art communication techniques, such as light and radar communication, which are rapidly reaching market maturity. Selecting the appropriate technology for every application is a general question that needs to be addressed on an individual basis. Industry and research must work together closely to develop the solutions of the future.